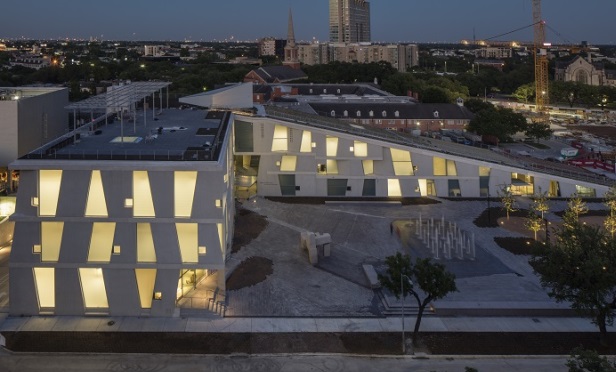
HOUSTON—Phase I of the expansion project for the Museum of Fine Arts, Houston, Texas' oldest museum, has been completed. This phase of the project includes a new 80,000-square-foot Glassell School of Art.
McCarthy Building Companies Inc. is the construction manager at-risk and has worked with the design team, Steven Holl Architects, from the beginning of the project to ensure the vision for the school came to life. McCarthy utilized innovative technologies to construct models and plan for the unique project challenges, features and materials.
“McCarthy is pleased to be the general contractor on such an architecturally unique and important project such as the Museum of Fine Arts, Houston that will offer a lasting legacy to the city,” said Jim Stevenson, McCarthy Houston division president. “We collaborated with the entire project team to ensure the challenges posed by such unique designs were carefully and strategically considered and approached.”
The Glassell School of Art is now double in size and will serve more than 7,000 students each year. The school's addition includes a studio school for adults, a junior school with classes for students ages 3 to 18, and the core residency program for post-graduate artists and critics. The school links to two existing gallery buildings and a sculpture garden as part of a redevelopment of the 14-acre Susan and Fayez S. Sarofim Campus.
The puzzle design of the new Glassell School of Art made the building as much a piece of art as the art displayed within the museum. The hybrid material structure provided for a unique construction challenge. The building features 177 precast panels, with no two panels the same shape and 139 massive glass windows, each with a unique size and trapezoidal shape–either straight or at a 10-degree slant in-or-out.
“It is uncommon to put these elements together, and no one wanted to do it,” says Brian Luney, project director for McCarthy, “So McCarthy self-performed the cast-in-place concrete work.”
McCarthy incorporated advanced technology and building methods including LEAN principles, laser scanning and building information modeling/BIM to maintain quality on the job site, and save time and money. BIM helped create virtual reality models allowing the museum to see the building before construction and assist in decision making. Additionally, teams used 3D MEP coordination to allow for better placement of devices from an architectural standpoint, ultimately helping the client track placement of all building elements for future repairs and renovations.
“McCarthy is leading the construction industry by employing a multitude of technology innovations to enhance building efficiencies including the use of virtual reality,” Stevenson tells GlobeSt.com. “Like that used in the design and preconstruction phase of the Museum of Fine Arts, Houston, VR ensures a higher level of confidence in the design and outcome of the project.”
McCarthy has a history of building complex, architecturally significant projects in the entertainment and arts industry. In addition to the Museum of Fine Arts, Houston, McCarthy's Texas portfolio of entertainment and institutional projects includes the AT&T Performing Arts Center Dee and Charles Wyly Theatre in Dallas, the Dallas City Performance Hall, and the Kinder High School for Visual and Performing Arts in Houston, among others.
© Touchpoint Markets, All Rights Reserved. Request academic re-use from www.copyright.com. All other uses, submit a request to [email protected]. For more inforrmation visit Asset & Logo Licensing.